The Mystery of Automatic Lubricators Is Revealed
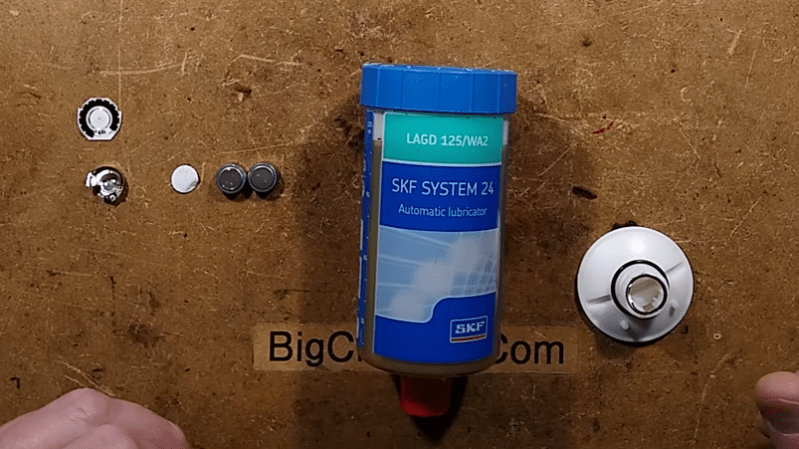
Industrial machines have all kinds of moving parts that require regular lubrication in order to prevent wear and damage. Historically, these would require regular visits from maintenance personnel to keep them greased up and slippery. Automatic lubricators eliminate that job by regularly dosing machines with fresh grease, and [Big Clive] decided to see what makes them tick.
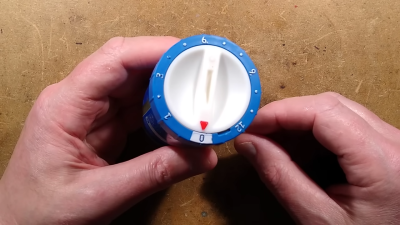
The simplest models merely use a spring to slowly force grease out over time. Changing the spring changes the rate at which grease is dispensed. Chemical versions exist too. A chemical pill is selected and inserted into a chamber with liquid, which releases gas over time. As gas is released, it creates pressure which forces a plunger down, dispensing grease over time.
Perhaps the fanciest versions are the electronic models, however, which have a dial on the back for selecting the rate of grease delivery. Turning the dial changes a resistance that is connected across two zinc-air cells which are sealed. Apparently, when current is forced through these cells and they’re excluded from oxygen, the cells liberate hydrogen gas, according to a patent [Big Clive] found. This then forces down the plunger, dispensing the grease. Turning the dial changes the resistance, changing the rate at which grease is dispensed.
The quest for labor saving in industry has produced multiple designs of automated lubricator, all of which are fantastically simple and optimised for purpose. It shows just how much can be achieved with a few components and some creative thinking, where one’s first impulse might be to reach for a timer or microcontroller to do the job.
Lubrication is incredibly important – don’t forget it when building your CNC machines! Video after the break.
[Thanks to hackbyte for the tip!]
Post a Comment