Explosion Welding Goes Off With A Bang
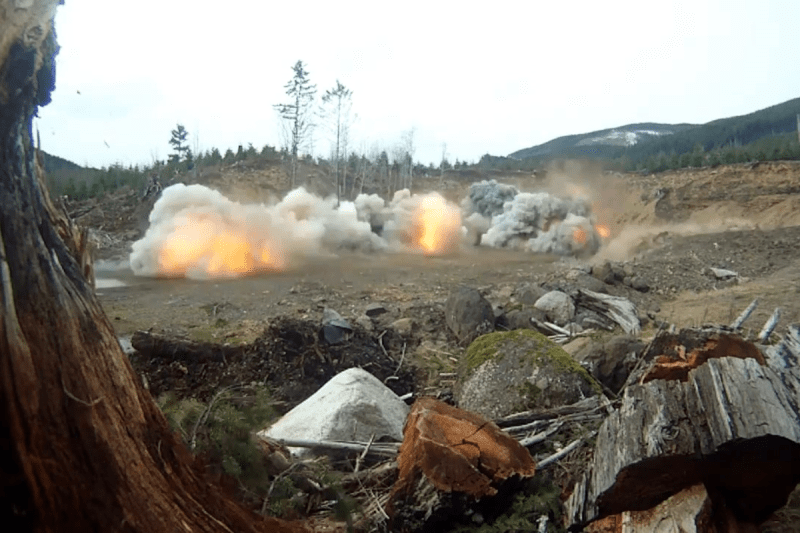
Welding is often a hot and noisy process. It generally involves some fancy chemistry and proper knowledge to achieve good results. Whether you’re talking about arc, TIG, or MIG, these statements all apply.
The same is true for explosion welding, though it’s entirely unlike any traditional hand welding methods you’ve ever seen before. Today, we’ll explore how this technique works and the applications it’s useful for. Fire in the hole!
Don’t Blow Them Apart, Blow Them Together!
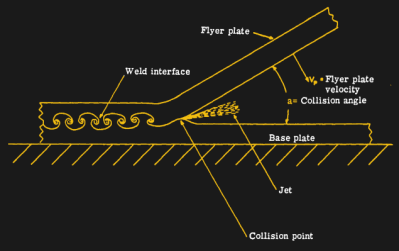
The technique of explosion welding is relatively new compared to other metal-joining techniques. In the two World Wars of the 20th century, pieces of shrapnel were often found stuck to armor plating. Close observation showed that shrapnel was in fact welding on to metal armor, rather than simply being embedded in such. Given that collisions between shrapnel and armor often occur without the extreme heat of typical welding operations, it indicated that it was instead great velocity of the impact between shrapnel and armor that was melding the metals together.
The same results were later recreated in the lab, and explosoin welding was developed into a refined technique after World War II. 1962 saw DuPont patent a process for explosion welding later to be known under the “Detaclad” trademark.
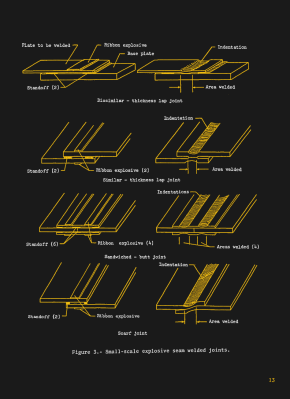
Explosion welding occurs with the metal remaining in the solid phase, so this is referred to as a “solid-state” welding technique. In its most common form, a thick metal plate known as the “backer” is laid flat, with spacers on the order of an inch or less placed on top. A thinner metal plate, known as the “cladder” is then placed on top of the spacers, such that there is a small gap between the two plates to be welded together. The two plates are ground flat prior to joining, in order to remove impurities and guarantee a quality weld.
Explosive powder is then packed on top of the cladder. The powder charge is typically detonated starting from one or corner or side of the cladder. This creates a sweeping effect through the explosive charge, with the explosion front moving across the top of the cladder at a uniform rate. This progressively forces the cladder into contact with the backer below. This process generates a plasma jet of air, oxides, and impurities that is shot out ahead of the closing gap between the two plates, cleaning the surfaces of the plates as it goes.
The resulting weld is caused by the plastic deformation of both metals, rather than by their liquification as is typical in traditional welding processes. These bonds can have up to 100% of the strength of the parent material, and typically have less issues around heat-affected areas compared to liquid-phase welding techniques. The results are similar in this regard to those achieved with friction welding. The two metal plates are joined in a continuous and uniform fashion across their entire surface.
The process enables dissimilar metals to be welded together. This even includes odd combinations like steel and aluminium, and even some reactive metals. Companies that specialize in the technique typically quote lists in excess of 260 different metal combinations that can be bonded in this manner.
Of course, due to the violence of the explosive reaction, explosion welding is typically limited to plates and simple cylindrical forms. The technique is often used to create tubes or tanks with clad metal surfaces for use in chemical and petrochemical industries. Explosion welding was even used in the Apollo spacecraft, which relied on the process to create a strong titanium-to-steel transition joint.
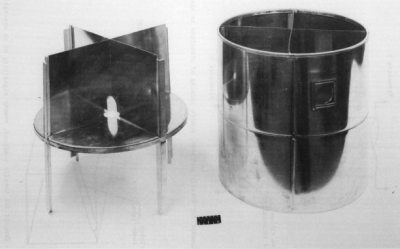
The space agency even published a technical memorandum on the topic in 1983, sharing details on Practical Small-Scale Explosive Seam Welding. The techniques involved relied on RDX explosives to create long, uniform joints that were of such high, consistent quality as to be hermetically sealed. The paper notes that the technique was applied to the repair of nuclear reactors in Canada, though it could also be used in other situations such as sealing pipelines or other vessels.
Given the use of high explosives, it’s not a technique that’s particularly easy to DIY in the home garage. However, if you find yourself needing to stick a plate of one metal to a completely different one to build something with useful combined properties, explosion welding might just be the tool you need. Just be sure to do it somewhere safe and far away, and to call out before you hit the detonator!
[Header image: Still from “Explosive Welding“, JRP RC Judd Phillips]
Post a Comment