Anodizing Titanium in Multiple Colors
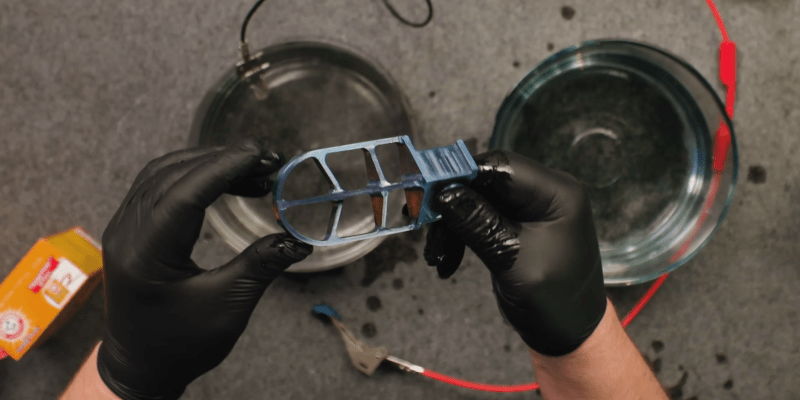
[Titans of CNC Machining] wanted to anodize some titanium parts. They weren’t looking for a way to make the part harder or less prone to corrosion. They just wanted some color. As you can see in the video below, the resulting setup is much simpler than you might think.
The first attempt, however, didn’t work out very well. The distilled water and baking soda was fine, as was the power supply made of many 9V batteries. But a copper wire contaminated the results. The lesson was that you need electrodes of the same material as your workpiece.
In this case, they happened to have some handles made of titanium, but some stock pieces would probably work, too. Your eye sees light reflecting from both the oxide layer and the underlying titanium at different angles. Because those reflections interfere with each other, they either cancel each other out or combine. That’s what makes it appear to be a color. By changing the voltage, you can get different oxide thickness and, therefore, different colors.
This is type III titanium anodizing, so it is common to see this used for identifying parts quickly. For example, bone screws for orthopedic surgery are typically treated this way, so the surgeon can ask for a “green screw” instead of a specific size. Because of the way the interference works, you can’t make every color. For example, there is no red anodized titanium. Parts anodized using Type II, on the other hand, have a telltale gray color. They are more resistant to wear and corrosion.
We’ve covered several ways to do aluminum anodizing before. If you are short on baking soda, you can always try Coke Zero.
Post a Comment