How Graphene May Enable The Next Generations Of High-Density Hard Drives
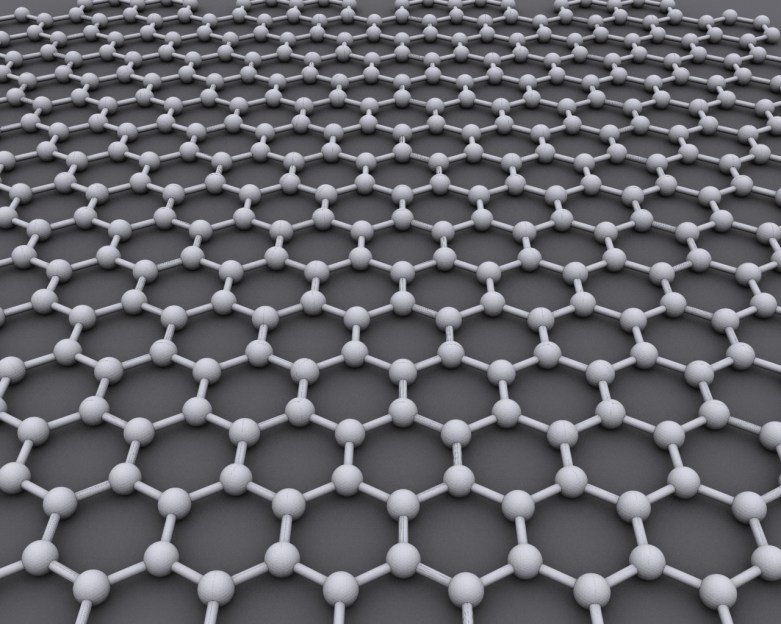
After decades of improvements to hard disk drive (HDD) technology, manufacturers are now close to taking the next big leap that will boost storage density to new levels. Using laser-assisted writes, manufacturers like Seagate are projecting 50+ TB HDDs by 2026 and 120+ TB HDDs after 2030. One part of the secret recipe is heat-assisted magnetic recording (HAMR).
One of the hurdles with implementing HAMR is finding a protective coating for the magnetic media that can handle this frequent heating while also being thinner than current coatings, so that the head can move even closer to the surface. According to a recent paper by N. Dwivedi et al. published in Nature Communications, this new protective coating may have been found in the form of sheets of graphene.
The Need for a Protective Coating
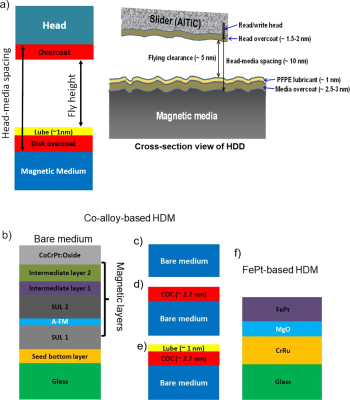
Perhaps the irony in calling HDDs ‘spinning rust’ is that the process of corrosion is one of the major enemies to the long-term operation of these devices. The thin magnetic layer on top of a platter’s base material would readily corrode if left exposed to an atmosphere. Cobalt, the Co the CoCrPt alloys, is especially susceptible to this process. Once corroded, that part of the platter would then be far less effective at retaining a magnetic orientation. One of the primary purposes of this coating, or overcoat, is to prevent this from happening.
The other use of the overcoat is as a protective measure against mechanical damage. Despite all the fright about ‘head crashes’, mechanical contact with the platter is fairly common, and one of the uses of the overcoat is to provide protection against this, as well as reduce friction. The latter usually involves the use of lubricants, which adds another layer on top of the overcoat. Together with the overcoat, the lubricant layer forms a significant part of the head-media spacing (HMS), and thus how close the head can get to the recording media.
In order for the areal density (AD) of hard drives to keep increasing, it’s necessary for this HMS to decrease even further, which means a thinner overcoat. Today these are carbon-based overcoats (COCs), generally between 2.5-3 nm thick. For upcoming high-density magnetic media that is compatible with HAMR, this means that the COC has to fulfill the following requirements:
- Provide all features with a <1 nm coating
- Full corrosion protection
- Anti-friction equivalent to current COCs
- Wear resistance and stretch resistance (elasticity, i.e. Young’s Modulus)
- Lubricant compatibility (e.g. PFPE).
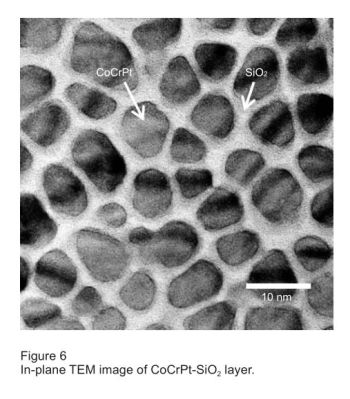
Of note here is that the magnetic recording material itself is also likely to change during the transition from PMR (perpendicular magnetic recording) to HAMR. This is similar to what happened during the transition from linear magnetic recording (LMR) to PMR as detailed in this paper by I. Kaitsu et al. from 2005.
With LMR, platters had used a coating of CoCrPt for the magnetic media, but for PMR this coating had to be more granular. The solution here was found in adding SiO2, as its grain boundaries neatly subdivide the CoCrPt into magnetic grains which work well with a PMR read/write head.
For HAMR magnetic media, the platter stack is changing again, this time to use FePt for the recording media, as this alloy is generally stable with the use of heat-based recording. This adds another two requirements to the coating for FePt-based platters:
- Thermally stable with HAMR cycles.
- Compatible with not only CoCrPt, but also FePt.
An ongoing issue with HAMR-based drives is that the application of local heat rapidly degrades the COC. Finding a new, more thermally stable overcoat material is paramount in their further commercialization.
Eventually, films of FePt will likely give way to bit-patterned media (BPM), in which magnetic islands are patterned into the magnetic recording layer. This would be similar to the CoCrPt-SiO2 magnetic grains, only on an even smaller scale. Ideally, the same <1 nm COC that works with FePt will also work with such new and upcoming technologies.
The Many Faces of Carbon
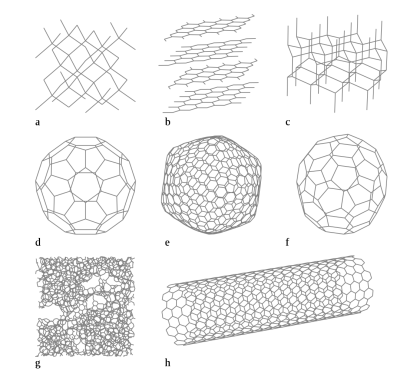
As the name of COC indicates, it too is based on carbon atoms, just like graphene. So what’s the difference between current COCs and new, graphene-based COCs? The main difference is in the way that the carbon atoms are linked together, also known as the allotropes of carbon. In graphene, the carbon atoms are linked together in a regular hexagonal lattice.
This regular lattice is part of the reason why graphene is so stable, but producing it has been a major challenge for a long time. It wasn’t fully isolated and characterized until 2004, when Andre Geim and Konstantin Novoselov at the University of Manchester used the world-famous ‘Scotch tape’ technique to pull graphene layers from graphite.
Since that time, the search for commercial applications of graphene has been ongoing, with the use in HDD COCs one of the more recent ones. As a two-dimensional material that is thermally and otherwise stable, it seems rather ideal for any situation where full coverage of a surface is required. Even if said surface is regularly being blasted by a laser as in the case of HAMR-based hard disk drives.
Science Checks Out
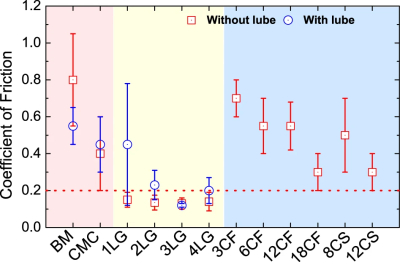
After N. Dwivedi et al. used chemical vapor deposition (CVD) to coat the bare media with 1-4 layers of graphene (1-4LG) using a wet transfer process. They then subjected these graphene COCs along with existing commercial COCs to various tests, including mechanical (friction and wear), laser-based heating and corrosion protection.
Although even a single layer of graphene (1LG) managed to significantly reduce corrosion and show good mechanical, friction, and thermal stability properties, it was found that >2LG-based coatings would likely provide the greatest benefit. Not just with existing CoCrPt-SiO2 media, but also with FePt with HAMR, and HAMR plus BPM. What this essentially means is that a >2LG COC should be suitable for hard drives today and well into the future.
Another interesting finding was that graphene-based COCs do not require lubrication as do current commercial COCs. The benefit of this is that commercially used PFPE lubrication in hard disk drives is not thermally stable when used with HAMR, and thus being able to omit it in favor of just the heating-resistant graphene means that two problems are solved simply by using >2LG instead of non-graphene COCs.
It’s the Little Things
The most interesting thing about this paper is an insight in how the development of new technologies is often held up by what seems like small details. Even though a suitable magnetic recording media was found in FePt already, and even though integrating semiconductor lasers in read/write heads was already a more or less solved problem, the lack of a suitable overcoat material could have derailed all of that effort, or at least postponed it for years.
We can’t celebrate and put in orders for HAMR HDDs just yet, of course. The fun part with materials science comes after a concept has been demonstrated in the laboratory and it has to be scaled up to mass-production. There’s a massive difference between the CVD of graphene in laboratory settings to produce a few platters for a test and producing thousands upon thousands of them in an automated factory setting.
There are a dizzying amount of ways to produce graphene at this point, which is both good and bad news. Not all methods create the same quality graphene, and not all methods lend themselves to mass-production, or the integration into the hard drive manufacturing process. Figuring out the best way to take the results from this recent paper and make it work in a factory setting will be the next step, which can take many more years.
But as with all things in science, good things come to those who are patient.
(Heading image: visualization of single sheet of graphene. Credit: AlexanderAlUS, CCA-SA 3.0)
Post a Comment